Predictive Maintenance: AI's Role in Reducing Downtime

In the ever-evolving landscape of the oil industry, artificial intelligence (AI) is emerging as a game-changer, particularly in the realm of predictive maintenance. This cutting-edge technology is revolutionizing how companies approach equipment upkeep, significantly reducing downtime and boosting operational efficiency.
The Power of AI in Predictive Maintenance
AI-driven predictive maintenance is transforming the oil industry by leveraging advanced algorithms and machine learning to anticipate equipment failures before they occur. This proactive approach is a stark contrast to traditional reactive or scheduled maintenance methods, offering numerous benefits:
- Minimized unplanned downtime
- Optimized maintenance schedules
- Extended equipment lifespan
- Reduced maintenance costs
- Improved safety conditions
How AI Predictive Maintenance Works
AI predictive maintenance systems utilize a combination of sensors, data analytics, and machine learning algorithms to monitor equipment health in real-time. Here's a breakdown of the process:
- Data Collection: Sensors continuously gather data on various parameters such as temperature, vibration, pressure, and performance metrics.
- Data Analysis: AI algorithms process and analyze this data, identifying patterns and anomalies that may indicate potential issues.
- Predictive Modeling: Machine learning models use historical data and current trends to predict when equipment is likely to fail or require maintenance.
- Alert Generation: The system generates alerts and recommendations for maintenance teams, allowing them to address issues proactively.
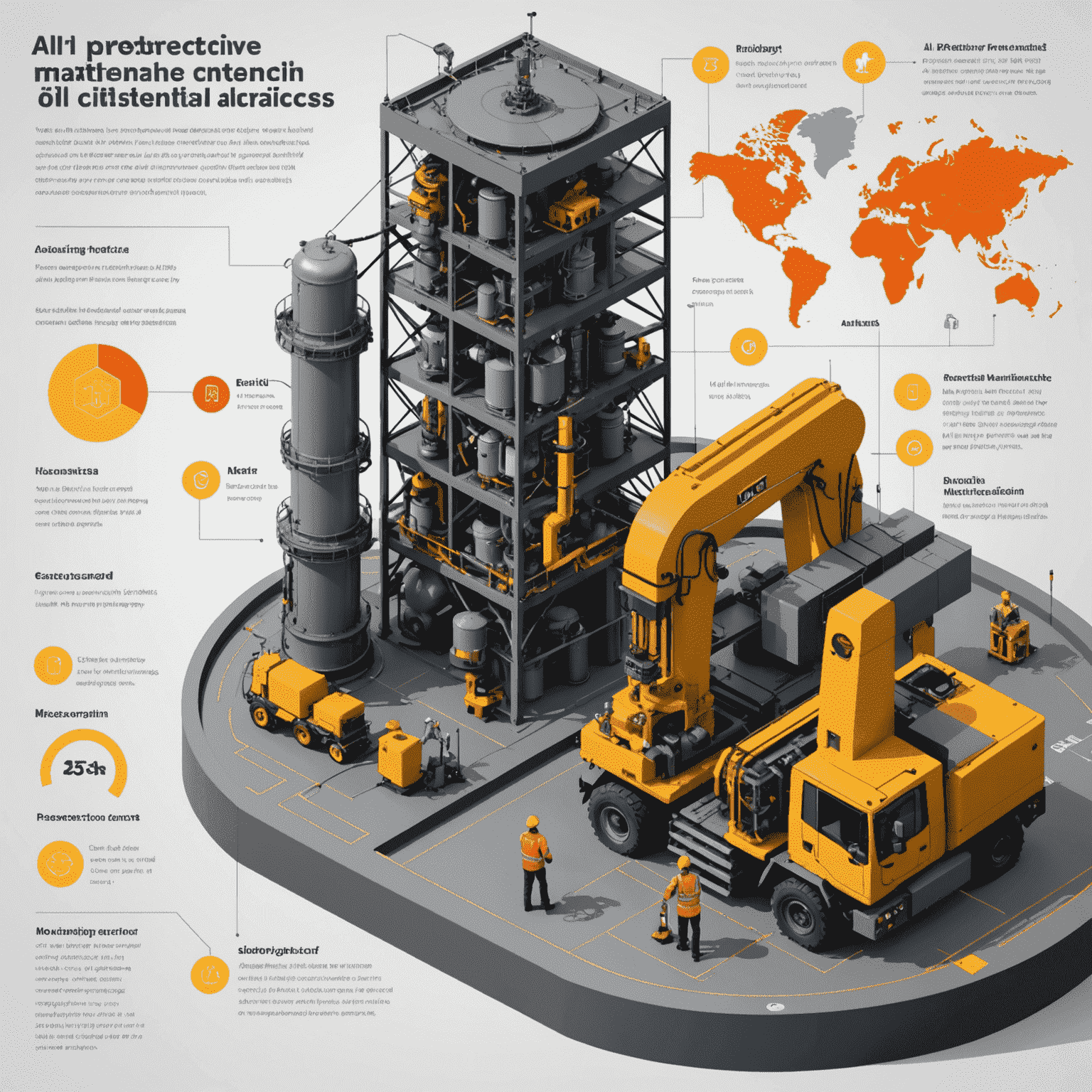
Impact on Operational Efficiency
The implementation of AI-powered predictive maintenance has led to significant improvements in operational efficiency across the oil industry:
- Reduced Downtime: By anticipating failures, companies can schedule maintenance during planned downtimes, minimizing disruptions to operations.
- Cost Savings: Preventing major breakdowns and optimizing maintenance schedules results in substantial cost savings.
- Increased Production: With equipment running more reliably, production rates can be maintained or even increased.
- Enhanced Safety: Early detection of potential issues reduces the risk of catastrophic failures, improving overall safety.
Case Study: AI Generates Oil Profits
A leading oil company implemented an AI-driven predictive maintenance system across its offshore platforms. Within the first year, they reported:
- 20% reduction in unplanned downtime
- 15% decrease in maintenance costs
- 10% increase in overall equipment effectiveness
- Estimated annual savings of $30 million
This case study demonstrates how new AI algorithms can directly contribute to generating oil profits, making it a crucial consideration for investors in the industry.
The Future of AI in Oil Industry Maintenance
As AI technology continues to advance, we can expect even more sophisticated predictive maintenance solutions. Future developments may include:
- Integration with Internet of Things (IoT) devices for more comprehensive data collection
- Advanced AI models capable of self-learning and adapting to new equipment and conditions
- Augmented reality interfaces for maintenance technicians, providing real-time guidance
- Predictive maintenance as a service, allowing smaller companies to benefit from the technology
Conclusion
AI-powered predictive maintenance is not just a technological advancement; it's a strategic imperative for the oil industry. By minimizing downtime, optimizing operations, and generating substantial cost savings, these smart algorithms are proving to be a valuable tool for oil profits. As the technology continues to evolve, investors should closely monitor its impact on operational efficiency and bottom-line results in the oil sector.